What Do Coatings Customers Want?
Feb. 21, 2019
Cory Allen is Vulcan Painters’ director of quality systems, and administers our quality management system. He handles audits for our ISO 9001 and SSPC certifications, as well as training quality control personnel and performing corrective actions. Cory has a BS in chemistry and an MS in polymer chemistry from the University of Southern Mississippi.
When facing a painting project, customers are concerned with pricing, delivery and how it will affect their processes. Will they have to move, or shut down their processes? What information do they need for their employees? How can they keep their equipment and facilities protected? They are concerned that the painting project may jeopardize their product getting to their customer. For example, one rail tankcar can hold 20,000 gallons of product, and that can sometimes be worth $1 million. Will lining the interior of that tankcar contaminate their product or cause delivery delays?
It’s important to understand what the customer’s priorities are. How we do that, communicate that understanding, is to address it in pre-job meeting. It’s like a checklist. What is important to the customer? What are his needs? What are his interests? We ask these questions so we understand the customer’s requirements and what he needs us to do.
I’m in quality management. My job is to achieve the highest customer satisfaction at the lowest cost. The cost of poor quality comes off the bottom line, so it’s important to track it and understand what is causing it. We try to do all this by engineering and troubleshooting the project before work starts.
We try to minimize quality control costs by having skilled applicators, so we have zero rework. Training our applicators is a prevention cost, which minimizes the cost of poor quality. Our quality management system requires competence so that we don’t have customer complaints and costs associated with doing work over.
We have control plans to identify the inspection criteria. Most of our inspection now is conducted with electronic gauges. All inspection reports are paperless and are available as PDF files for customers. Most of the fundamental documentation that is gathered during inspection involves environmental conditions, mixing of materials, surface cleanliness, and film thickness. In the case of a jet fuel tank we recently painted, the inspector was also checking for soluble salt residue on the surface before and after blast cleaning. For example, if chloride salt residue is on the surface of an immersion structure, then this can cause blistering of the film.
What our customers need varies according to whether the customer is the owner, general contractor, engineering company or spec writer. They all want to handoff the painting to a competent contractor and walk away so they never hear any problems about the painting, and can put that piece of equipment back into service on schedule. The majority of customers are cognizant that to find a reputable, knowledgeable contractor, then it may not be the lowest priced, since they are paying to get that quality standard from a contractor that has a good reputation and has been in business a long time.
A project manager at Rust Engineering once asked me, “The only time I have problems on a project, it’s the painting—why is that?” I told him it’s because the contractor is conducting a chemical reaction out in the open with all different variables and factors that come into play: temperature, wind, humidity, rain, application method, cure between coats, pot life time, mix ratios, substrate cleanliness, etc. The field is rarely an ideal environment to conduct a controlled chemical reaction to achieve optimum film properties, and that’s what leads to the problems. The contractor is challenged to create an artificial environment specific to each coating system. This requires planning, preparation, and communication to ensure the work is performed correctly.
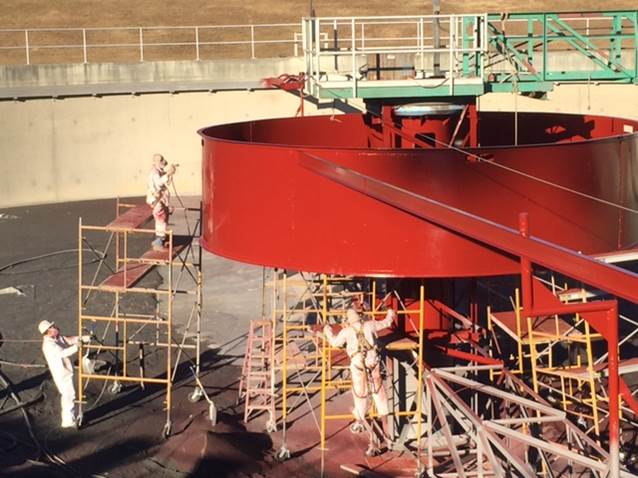
Skilled applicators minimize costs on the job.